Techniques and Services that Prevent Corrosion in Gulf Coast Pipelines
Due to the region’s high humidity, salt-laden air, and fluctuating temperatures, pipelines in the Gulf Coast area are vulnerable to rust, pitting, and other forms of corrosion. Here is a brief breakdown of effective techniques and services that can prevent corrosion, protect assets, and ensure the smooth operation of Gulf Coast pipelines.
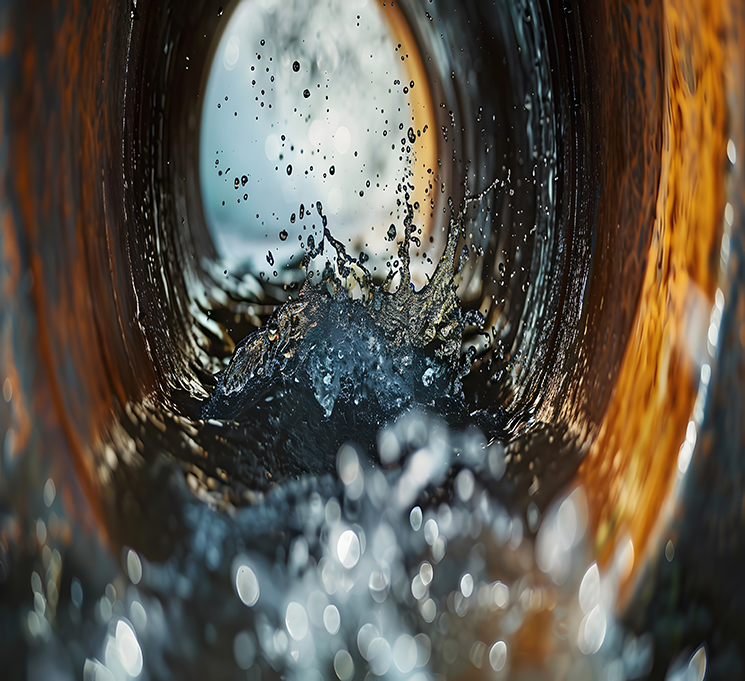
What Causes of Pipeline Corrosion on the Gulf Coast
Corrosion occurs when metals in the system react with environmental elements like oxygen, moisture, or an incompatible chemical. This causes a chemical reaction that weakens the metal’s structure. This can lead to issues like
- Rust
- Pitting (pits and holes eaten into the metal surface)
- Warping of parts, pipes, and filters
- Leaks and burst pipes
- Clogs from debris breaking off the system into the pipeline
- Product quality issues as the corrosion mixes with the transported material
Salt acts as a conductor, making it easier for metals to lose electrons and corrode. Gulf Coast sites exposed to salt water through the environment, storms, saltwater intrusion, and other means are vulnerable to accelerated effects of corrosion. The rapid temperature swings can also strain the pipelines and expose surfaces to corrosive elements.
Cathodic Protection Shields Pipelines from Electrochemical Reactions
Cathodic protection (CP) is an anti-corrosion technique that makes the pipeline the “cathode” of an electrochemical cell. This technique typically involves two methods.
- Sacrificial Anode. Reactive materials like zinc or magnesium are attached to the pipeline. These anodes corrode in place of the pipeline, “sacrificing” themselves to protect the pipeline from corrosion.
- Impressed Current Cathodic Protection (ICCP). An external power source directs a controlled electrical current toward the pipeline to neutralize corrosive reactions. This system is ideal for larger pipelines or high-risk areas prone to extreme corrosion.
These methods shield the metal surface, which extends the pipeline’s operational life and reduces maintenance needs.
Oil Flushing Removes Contaminants to Prevent Internal Corrosion
Oil flushing helps prevent corrosion inside pipelines. It cleans the pipeline’s interior by circulating oil at a high flow rate to dislodge rust and debris that could lead to pitting and internal corrosion.
PSI takes this a step further by deploying vibrators to the piping circuit to reduce the overall flush duration. This process removes contaminants like debris, rust, sludge, and other unwanted particles from your lube or hydraulic system pipes and equipment.
Pipeline Coatings Create a Physical Barrier Against the Elements
Specialized coatings create a barrier between the pipeline and corrosive elements. Several types of protective coatings are commonly used on Gulf Coast pipelines.
- Fusion Bonded Epoxy (FBE) Coatings are highly durable, heat-resistant, and effective at protecting pipelines from moisture and salt. They are applied as a dry powder that bonds with the pipeline’s surface when heated, forming a tough protective layer.
- Polyurethane Coatings are highly flexible and impact-resistant. They are often used in regions with shifting temperatures, as they resist cracking and peeling. They also provide a solid shield against environmental damage and Gulf Coast humidity.
- Polyethylene Wraps are applied as a tight-fitting jacket around the pipeline, preventing contact with corrosive elements and offering an additional layer of protection.
Applying these coatings can prevent surface corrosion and reduce the need for frequent maintenance in high-risk areas.
Desiccant Drying Controls Moisture to Reduce Internal Corrosion
Desiccant drying is a preventive technique that reduces moisture in the pipeline by using materials that absorb water. By filling sections of the pipeline with desiccants, moisture is removed from the interior, lowering the risk of rust and other forms of internal corrosion.
This method is often applied after hydrostatic testing or in newly constructed pipelines to ensure the interior remains dry and corrosion-free.
Internal Linings Defend Against Internal Corrosion
Internal linings are a barrier between the metal and the transported materials. This helps protect the pipes from things like
- Rust
- Debris
- Corrosive or abrasive transported materials
Cement, epoxy, and polymer coatings are common lining materials. Each offers unique protective benefits suited to specific materials transported in pipelines. Choosing the right one for your system can significantly increase the lifespan of your pipes and downstream equipment.
Conclusion
Corrosion is an unavoidable challenge for Gulf Coast pipelines, but it can be managed with the right preventative measures for your situation. Contact us today to learn how our comprehensive pipeline services can help protect your Gulf Coast assets from corrosion, reduce maintenance costs, and extend the lifespan of your pipelines.